在现代工业环境中,生产流程效率分析成为企业提高竞争力的关键手段。许多公司面临着如何优化生产流程、减少浪费的挑战。尽管大多数企业都意识到这些问题,但真正的解决方案并不总是显而易见。实际上,对生产流程进行深入分析常常揭示出一些反直觉的事实,例如,有时增加某些步骤反而能整体提升效率,或者某些长期使用的流程竟然是浪费最大的问题所在。这篇文章将深入探讨如何进行生产流程效率分析及优化流程的方法,帮助企业减少浪费,提高生产效率。

📊生产流程效率分析基础
生产流程效率分析是复杂的工作,涉及多个维度的数据评估和流程观察。为了有效开展分析,首先需要理解生产流程的各个方面,包括时间、成本、资源利用率等。下面我们将详细分解这些关键步骤。
1. 识别关键流程节点
第一步是识别生产流程中的关键节点。这些节点通常是流程中的瓶颈或资源密集区。识别这些节点可以通过观察生产线或使用数据分析工具进行精确定位。FineBI作为新一代自助大数据分析工具,能够快速搭建企业的自助分析平台,帮助识别这些关键节点。
在识别节点时,不妨考虑以下几个方面:
- 时间消耗:哪个节点耗时最长?
- 资源使用:在哪些节点资源使用最密集?
- 等待时间:在哪些节点等待时间最长?
关键节点 | 时间消耗 | 资源使用 | 等待时间 |
---|---|---|---|
A | 高 | 中 | 高 |
B | 中 | 高 | 低 |
C | 低 | 中 | 中 |
2. 数据收集与分析
一旦识别了关键节点,下一步是收集相关数据,并进行深入分析。数据收集包括生产时间记录、成本分析、质量检查等。通过这些数据,可以找到潜在的改进点。
在进行数据分析时,推荐使用FineBI来提高分析效率。FineBI不仅支持多维度数据分析,还可以构建统一指标中心,支撑自助分析、看板制作等功能。
数据分析的常用方法包括:
- 回归分析:识别影响生产效率的主要因素。
- 时间序列分析:观察生产指标的变化趋势。
- 成本效益分析:评估不同改进方案的投入产出比。
🔍优化生产流程的方法
在完成生产流程效率分析后,下一步是优化生产流程。优化流程不仅仅是减少浪费,还包括提高生产速度和产品质量。
1. 流程简化与自动化
流程简化是指剔除不必要的步骤,优化流程路径。在进行简化时,自动化也是一个重要的考虑因素。通过自动化,企业可以大幅度降低人力成本,提高生产效率。
自动化可以应用于以下几个方面:
- 物料搬运:使用自动化设备减少人工搬运。
- 质量检测:通过机器视觉或传感器实时检测产品质量。
- 信息传递:使用数字化平台进行实时信息共享。
优化方面 | 简化措施 | 自动化应用 |
---|---|---|
搬运 | 路径简化 | 自动设备 |
检测 | 步骤减少 | 机器视觉 |
信息 | 流程简化 | 数字平台 |
2. 持续改进与员工参与
优化生产流程并不是一次性的任务,而是一个持续改进的过程。通过员工的参与,企业可以获得更多的改进建议和支持。在持续改进过程中,员工的反馈至关重要。
持续改进包括:
- 定期评估:每月或每季度对流程进行评估。
- 员工培训:提高员工技能以支持新流程。
- 反馈机制:建立员工反馈渠道以获取改进建议。
📈减少浪费的策略
减少浪费是生产流程优化的重要目标。浪费不仅意味着资源的无效使用,还可能导致生产成本的增加和产品质量下降。

1. 识别与分类浪费类型
浪费可以分为多种类型,包括时间浪费、物料浪费和能量浪费。识别浪费类型是减少浪费的第一步。
浪费类型包括:
- 时间浪费:冗长的等待时间。
- 物料浪费:过量生产或损坏。
- 能量浪费:设备闲置或效率低下。
浪费类型 | 识别方法 | 减少策略 |
---|---|---|
时间 | 时间记录 | 流程优化 |
物料 | 质量检查 | 精益生产 |
能量 | 能耗监控 | 设备升级 |
2. 实施精益生产
精益生产是减少浪费的有效方法之一。通过减少库存、优化生产计划和提高设备效率,精益生产可以显著降低浪费。
精益生产的策略包括:
- 库存管理:减少过多库存。
- 生产计划:优化生产计划以减少过量生产。
- 设备维护:定期维护设备以提高效率。
📚总结与展望
生产流程效率分析及优化是企业提升竞争力的重要手段。通过识别关键流程节点、优化流程、减少浪费,企业可以显著提高生产效率和产品质量。FineBI作为领先的大数据分析工具,为企业提供了强大的支持。
在未来,随着技术的不断进步,生产流程优化将变得更加智能和自动化。企业需要不断创新和调整策略,以应对市场变化和技术挑战。通过持续改进,企业能够在激烈的市场竞争中保持领先。
引用文献
- 《现代生产管理》,张伟,机械工业出版社
- 《精益生产理论与应用》,李强,人民邮电出版社
- 《大数据分析与应用》,王芳,电子工业出版社
通过综合使用这些策略和工具,企业能够有效提升生产流程效率,减少浪费,实现更高效的生产运营。
本文相关FAQs
🤔 如何有效地进行生产流程效率分析?
很多企业在提升生产效率时,往往会感到无从下手。老板要求我们用数据来分析生产流程的效率,但总觉得分析后也没有什么实质的改善。有没有大佬能分享一下怎么有效地进行生产流程效率分析?具体都需要关注哪些关键指标?
在进行生产流程效率分析时,了解关键指标至关重要。生产流程效率分析涉及多个维度,包括生产时间、资源利用率、质量控制等。首先,我们需要进行数据收集,这包括设备的运行时间、故障时间、生产产量等。通过这些数据,我们可以确定哪些环节最耗时,哪些设备故障频繁,以及在哪些环节可能存在资源浪费的问题。
步骤一:定义关键绩效指标(KPIs)
- 生产周期时间:衡量从开始到完成一个产品所需的时间。
- 设备利用率:计算设备的实际运行时间与可用时间的比率。
- 废品率:衡量生产过程中的产品不合格率,帮助识别质量控制问题。
步骤二:数据收集与分析 使用自动化工具进行数据收集能大大提高效率。例如,通过工业互联网平台收集设备数据,或通过ERP系统获取生产计划与实际生产数据。数据分析工具如BI工具,可以帮助我们快速地进行数据可视化和分析。推荐使用像FineBI这样的工具,它能够帮助企业快速构建自助分析平台: FineBI在线试用 。
步骤三:识别瓶颈与优化策略 通过数据分析,识别生产流程中的瓶颈环节。例如,某个设备故障频繁导致生产中断,那么需要考虑设备维护或升级。对于高废品率的环节,可以通过调整生产参数或工艺流程来改善。
案例分享 某制造企业通过FineBI进行数据分析,发现其某条生产线因设备老化导致效率低下。企业通过升级设备和优化工艺流程,将生产周期缩短了15%,废品率降低了20%。
通过以上步骤,我们可以更加系统、有效地进行生产流程效率分析,并制定相应的改善策略,从而达到优化生产流程、减少浪费的目的。
🛠️ 如何优化生产流程以减少资源浪费?
我们公司在生产过程中总是会产生大量的废料,老板要求我们优化生产流程以减少浪费。这方面有什么好的方法可以推荐?具体应该怎么操作呢?
优化生产流程以减少资源浪费,需要从系统的角度重新审视生产流程。资源浪费通常包括原材料浪费、时间浪费、以及设备和人力资源的低效利用。以下是一些实际操作建议:
识别并消除非增值活动 在生产过程中,非增值活动是指那些不直接增加产品价值的步骤,比如等待时间、运输时间等。要减少这些浪费,首先需要进行详细的流程分析,找出哪些步骤是非必要的。比如,通过引入智能物流系统,可以减少产品在生产线内的搬运时间。
实施精益生产 精益生产是一种通过消除浪费、提高效率的管理理念和方法。通过实施精益生产,可以更好地控制库存、减少不必要的生产步骤。例如,采用看板系统(Kanban)可以有效管理生产节奏,减少过量生产导致的库存积压。
自动化与数字化 自动化设备和数字化技术的应用也是减少浪费的重要手段。自动化可以减少人为操作带来的误差和资源浪费,而数字化技术可以帮助实时监控生产过程,及时发现并解决问题。
能源管理 除了物料浪费,能源浪费也是生产过程中常见的问题。通过引入能源管理系统,可以实时监控设备的能耗,优化设备运行参数,降低能耗。
案例分享 某家电制造企业通过实施精益生产和引入自动化设备,将生产线的非增值活动减少了30%,每年节省了大量的原材料和能源成本。
综上所述,优化生产流程以减少资源浪费需要从整体上重新设计流程,注重细节管理,运用现代化技术加以辅助。通过系统的改进,可以显著提高生产效率,降低生产成本,实现可持续发展。
📈 如何在优化生产流程的同时确保产品质量?
我们在尝试优化生产流程的过程中,产品质量有时会受到影响。有没有什么方法可以在提高生产效率的同时,确保产品质量不下降?
在生产流程优化中,产品质量的稳定是必须要考虑的关键因素。以下是一些确保在流程优化中保持产品质量的方法:
建立质量控制体系 质量控制体系的建立是确保产品质量的基础。在生产流程优化的同时,应加强质量控制环节。可以通过引入质量管理系统(QMS)来记录和分析质量数据,识别质量问题的根源,并迅速采取纠正措施。
加强员工培训 员工是生产过程中的重要参与者,加强员工培训可以提高他们的技能水平,降低因操作不当导致的质量问题。在优化流程时,应确保员工掌握新工艺和流程的操作要领。
引入自动化检测设备 自动化检测设备可以在生产过程中实时监控产品质量,发现质量问题后立即报警,避免不良品流入下游环节。比如,通过使用光学检测系统,可以实时检测产品的外观缺陷。
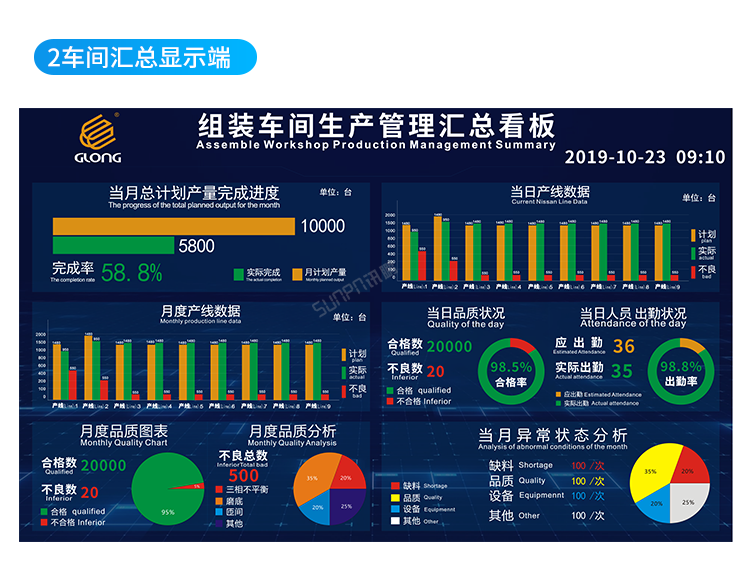
实施全面质量管理(TQM) 全面质量管理是一种以全员参与为基础的管理理念,强调从产品设计到生产的全生命周期质量控制。通过TQM,可以在流程优化中确保每个环节的质量标准。
案例分享 某电子产品制造商在优化生产线时,通过引入先进的自动化检测设备与全面质量管理体系,成功将不良品率降低了40%,并显著提高了客户满意度。
总之,在优化生产流程的同时,保持产品质量的稳定需要从质量控制、员工培训以及自动化检测等多个方面入手。通过系统化的管理和技术手段,可以实现效率与质量的双赢。