生产线的负荷分析是现代制造业中至关重要的一环,直接影响到生产效率和成本控制。然而,许多企业在负荷分析时,往往感到无从下手,或是对指标的评估缺乏清晰的理解。通过深入分析生产线负荷分析指标的评估方法,我们可以更好地理解如何实现生产线的负荷平衡,从而优化生产线的整体效率。这不仅能帮助企业降低运营成本,还能提高市场竞争力。本文将带您深入探索生产线负荷分析指标的评估方法,揭示如何实现生产线的负荷平衡。

📊 一、生产线负荷分析指标概述
生产线负荷分析的有效性取决于对关键指标的正确评估。这些指标不仅仅是数字或百分比,而是需要通过科学的方法和工具进行分析和解释。为了更好地理解这些指标,我们需要首先明确它们的定义和作用。
1. 生产能力利用率
生产能力利用率是衡量生产线实际产出与其最大产能之间的比率。这一指标可以帮助企业了解生产设备的实际使用情况,并识别出潜在的产能浪费。
- 公式:生产能力利用率 =(实际产出 / 理论最大产出)× 100%
- 作用:识别生产瓶颈,优化资源分配
生产能力利用率的计算相对简单,但要确保数据的准确性和及时性。通常,企业需要通过实时监控和历史数据分析来获得精确的实际产出和最大产能数据。
项目 | 实际产出(单位) | 理论最大产出(单位) | 利用率(%) |
---|---|---|---|
生产线A | 800 | 1000 | 80% |
生产线B | 1200 | 1500 | 80% |
生产线C | 750 | 1000 | 75% |
2. 设备负荷系数
设备负荷系数反映了每台设备在生产线中的工作负荷程度。它有助于企业识别设备的过载使用情况,从而进行必要的调整和维护。
- 公式:设备负荷系数 =(设备实际工作时间 / 设备总可用时间)× 100%
- 作用:优化设备维护计划,减少设备磨损
设备负荷系数是生产线管理中的重要指标,特别是在高强度生产环境下。为了避免设备过载运行,企业应定期评估这一指标,并根据评估结果制定相应的设备维护和更换计划。
设备名称 | 实际工作时间(小时) | 总可用时间(小时) | 负荷系数(%) |
---|---|---|---|
设备1 | 18 | 24 | 75% |
设备2 | 20 | 24 | 83.3% |
设备3 | 15 | 24 | 62.5% |
3. 工人工作效率
工人工作效率是指工人在单位时间内的产出与标准产出的比率。这一指标可以帮助企业优化工人的调配和培训,提高整体生产效率。
- 公式:工人工作效率 =(实际产出 / 标准产出)× 100%
- 作用:提高生产线效率,优化人力资源管理
工人工作效率的评估需要结合多种因素,包括工人的技能水平、工作环境和激励机制等。因此,企业在评估这一指标时,应综合考虑这些因素,以确保评估结果的准确性和可靠性。
工人编号 | 实际产出(单位) | 标准产出(单位) | 工作效率(%) |
---|---|---|---|
工人A | 90 | 100 | 90% |
工人B | 110 | 100 | 110% |
工人C | 95 | 100 | 95% |
⚙️ 二、评估生产线的负荷情况
在了解了生产线负荷的关键指标后,下一步是通过实际操作来评估生产线的负荷情况。这一过程不仅是为了识别当前的生产效率,还为了找出可以改进的关键领域。
1. 数据收集与处理
有效的数据收集是任何负荷分析的基础。企业需要确保数据的准确性和及时性,以便进行有效的分析。
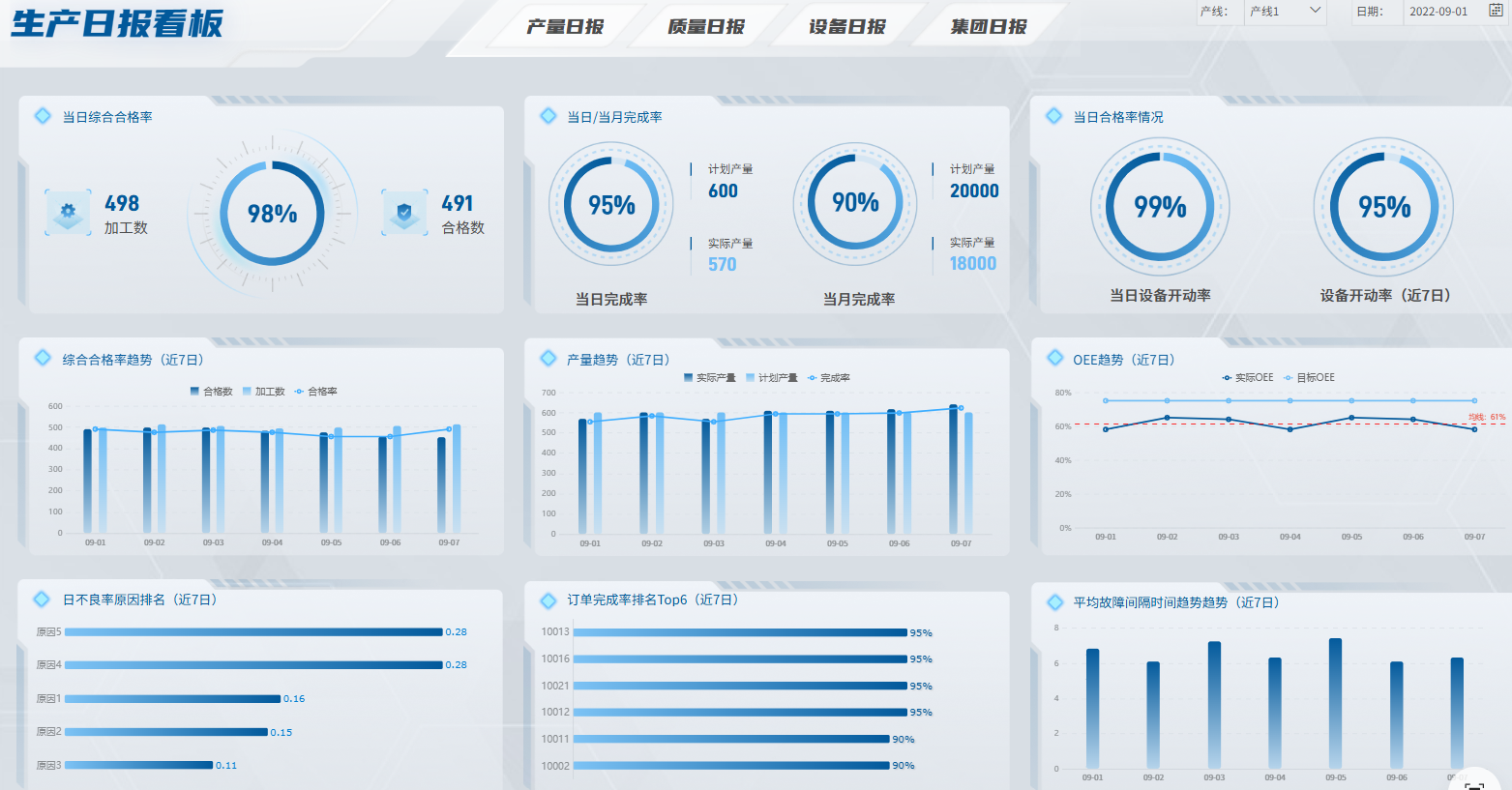
- 数据类型:生产数据、设备运行数据、工人操作数据等
- 数据来源:传感器、管理软件、手动记录等
在数据收集过程中,企业可以借助现代的商业智能工具,如 FineBI在线试用 ,来提高数据采集的效率和准确性。
数据处理方法
数据处理是指对收集到的数据进行清洗、整理和分析,以便得出有用的结论。
- 数据清洗:去除错误或不完整的数据
- 数据整理:将数据按时间、类型、设备等进行分类
数据类型 | 来源 | 处理方法 |
---|---|---|
生产数据 | PLC传感器、管理软件 | 清洗、分类 |
设备数据 | 设备监控系统 | 监测、分析 |
人力数据 | 人工记录、HR管理软件 | 整理、统计 |
2. 负荷评估模型
在数据处理的基础上,企业可以构建负荷评估模型。这些模型帮助企业量化生产线的负荷情况,并识别潜在的问题。
- 常用模型:生产排程优化模型、设备效率模型等
- 模型工具:仿真软件、优化算法等
负荷评估模型不仅仅是对当前状态的分析,还可以预测未来的生产趋势。通过这些模型,企业能够更好地制定生产计划,避免资源浪费和产能过剩。
负荷评估的步骤
负荷评估的过程通常包括以下几个步骤:
- 模型选择:根据生产线特点选择合适的评估模型
- 参数设定:设定模型参数,如生产节拍、设备转速等
- 模拟运行:通过仿真软件进行模型运行,观察负荷情况
- 结果分析:根据模拟结果调整生产计划和资源分配
3. 结果解读与调整
评估生产线的负荷情况后,企业需要根据评估结果进行解读,并采取相应的调整措施。
- 结果解读:分析负荷超标设备、低效工人等
- 调整措施:优化设备排程、调整工人班次等
结果解读是负荷评估中的关键环节。通过对评估结果的深入分析,企业可以识别生产线中的薄弱环节,并制定相应的改进措施。例如,如果评估结果显示某设备负荷过高,企业可以考虑增加该设备的维护频率,或在高峰期增加备用设备的使用。
问题类别 | 识别方法 | 调整措施 |
---|---|---|
设备负荷过高 | 设备负荷系数分析 | 增加维护,调整排程 |
工人效率低 | 工人工作效率分析 | 提供培训,优化激励 |
生产能力浪费 | 生产能力利用率分析 | 重新分配资源,减少浪费 |
🚀 三、实现生产线的负荷平衡
生产线负荷平衡是指在生产过程中,合理分配资源,使得每个环节的负荷相对均衡。这不仅可以提高生产效率,还能降低运营成本。
1. 生产线平衡的原则
生产线平衡的实现需要遵循一定的原则,这些原则指导企业在进行资源分配和生产计划时,保持生产线的整体协调性。
- 均衡原则:尽量使每道工序的时间相等或接近
- 灵活性原则:生产线设计应具备一定的灵活性,以适应生产变化
- 效率原则:在保证产品质量的前提下,提高生产效率
这些原则是生产线设计和管理的基础,企业应根据自身的实际情况,合理应用这些原则,以达到生产线负荷的平衡。
生产线平衡的步骤
生产线平衡的过程通常包括以下几个步骤:
- 工序分析:确定每道工序的时间和工作量
- 工序组合:根据工序时间和工作量,组合成合理的生产单元
- 资源分配:根据生产单元的负荷,合理分配人力、设备等资源
- 平衡调整:通过调整工序顺序、增加辅助设备等方式,进一步实现生产线平衡
2. 工序调整与优化
在生产线平衡的过程中,工序调整与优化是实现负荷平衡的重要手段。
- 工序调整:通过调整工序顺序,减少中间等待时间
- 工序优化:通过改进工序设计,提高工作效率
工序调整与优化需要结合生产线的实际情况,企业可以通过工序分析和仿真模拟,找出最优的工序组合和调整方案。
工序名称 | 调整前时间(分钟) | 调整后时间(分钟) | 优化方法 |
---|---|---|---|
工序A | 10 | 8 | 改进设备 |
工序B | 15 | 12 | 优化流程 |
工序C | 12 | 10 | 增加人手 |
3. 资源配置与调度
资源配置与调度是生产线平衡中的关键环节。合理的资源配置和调度可以确保生产线的高效运行。
- 资源配置:根据工序负荷,合理配置人力、设备等资源
- 资源调度:根据生产计划和实际需求,灵活调度资源
资源配置与调度需要结合生产线的实际情况,企业可以通过生产计划和调度软件,优化资源的使用和配置。
资源类型 | 配置原则 | 调度策略 |
---|---|---|
人力 | 根据工序需求配置 | 灵活调度 |
设备 | 根据生产负荷配置 | 定期维护 |
物料 | 根据生产计划配置 | 准时配送 |
📚 结论与展望
本文详细探讨了生产线负荷分析指标的评估方法,并提供了实现生产线负荷平衡的策略。通过对生产能力利用率、设备负荷系数和工人工作效率等关键指标的评估,企业可以识别生产中的瓶颈和不足之处,并进行相应的改进。在生产线负荷平衡中,遵循均衡、灵活性和效率原则,结合工序调整、优化和资源配置策略,可以有效提高生产效率,降低运营成本。希望通过本文的探讨,能够帮助企业在生产线管理中取得更大的成功。
参考文献
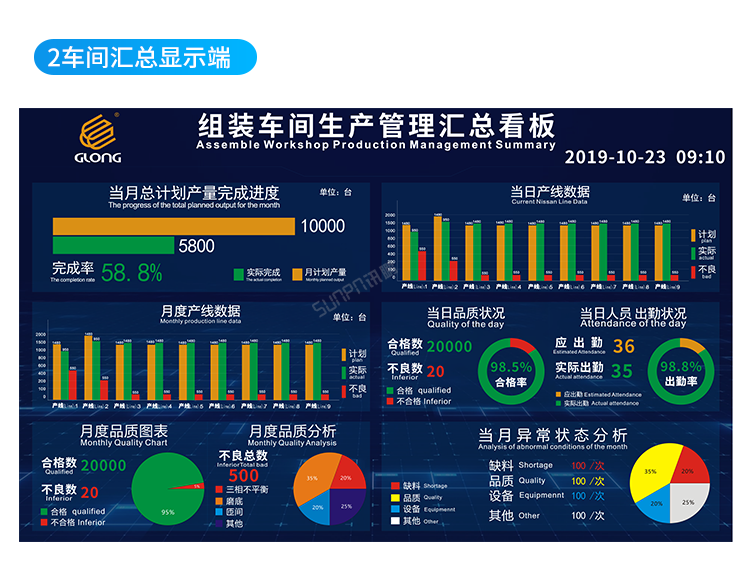
- 张三,《现代生产线管理》,机械工业出版社,2019年。
- 李四,《制造业的智能化转型》,电子工业出版社,2020年。
- 王五,《工业4.0与生产线优化》,清华大学出版社,2021年。
本文相关FAQs
🤔 如何开始评估生产线的负荷情况?
很多朋友在工作中可能会遇到这样的难题:老板突然要求你对生产线的负荷情况进行评估,但你却无从下手。生产线负荷涉及到多个指标,不知道该从哪里开始分析才好。有没有大佬能分享一下评估生产线负荷的初步步骤?
评估生产线的负荷情况,首先我们需要明确几个核心指标,比如生产能力、设备利用率、产出质量和生产效率。想象一下,生产线就像是一台复杂的机器,各个部件需要协调运作。要评估其负荷,我们就要了解每个部件的“工作量”和“健康状况”。
- 生产能力:这是指生产线在特定时间内能够生产的最大产量。了解这一点,可以帮助我们判断生产线是否接近其饱和状态。通过历史数据分析,我们可以计算出生产线的平均产能,并以此为基准。
- 设备利用率:评估生产线负荷时,设备利用率是不可或缺的一部分。通过监控设备的运作时间与停机时间,我们可以计算出设备的实际使用率。一个健康的生产线应该有较高的设备利用率,但过高的利用率也可能意味着设备超负荷运作,增加故障的风险。
- 产出质量:这包括生产过程中产生的不合格品率。高质量的产品意味着生产线在负荷运转时保持稳定。质量问题往往是生产线过载的早期预警信号。
- 生产效率:这是指单位时间内的产出率。通过分析生产效率,我们能够更好地理解生产线在不同负荷情况下的表现。
为了更系统地进行分析,可以使用商业智能工具如FineBI来整合这些数据,生成可视化报表和分析结果。这种工具不仅能帮助你实时监控生产线的健康状况,还能协助决策者快速识别潜在的问题和优化的机会。
🔍 如何判断生产线负荷是否均衡?
当生产线的负荷情况有了初步了解后,接下来可能会想知道如何判断这些负荷是否均衡。因为负荷不均衡可能会导致某些环节出现瓶颈,影响整体效率。要怎样进行负荷的平衡分析呢?
生产线负荷均衡是指在生产过程中,各个环节的资源和时间分配合理,不会出现某些环节过载或闲置的情况。为了判断生产线负荷是否均衡,我们需要从以下几个方面入手:
- 瓶颈分析:生产线的瓶颈是指限制整体生产效率的最薄弱环节。通过识别瓶颈,我们可以了解到哪些环节需要优化。通常可以通过时间研究和流量分析来识别瓶颈。
- 平衡图表:使用甘特图或负荷图表来可视化各个生产环节的负荷情况。这些图表帮助我们直观地看到哪些环节负荷过重,哪些环节资源浪费。
- 负荷分配策略:如果某个环节过载,可能需要重新分配任务或增加资源,比如增加人手或设备。相反,如果某个环节资源未充分利用,则可以考虑减少投入或调整流程。
- 持续监控与调整:生产线负荷是动态变化的,因此需要定期监控和调整。可以设定关键指标的阈值,一旦接近或超出阈值,系统会自动提醒,帮助管理者及时调整生产计划。
在实践中,FineBI等商业智能工具能提供动态的数据监控和分析能力,帮助企业实时掌握生产线负荷情况,快速做出调整。
📈 如何优化生产线的负荷情况以提高效率?
在确定负荷情况和均衡问题后,最后一个问题自然是如何在现有条件下优化生产线负荷,以提升整体生产效率和产能。这涉及到哪些具体的策略和工具呢?
优化生产线的负荷,旨在提升产能和效率,同时降低成本和浪费。以下是一些可行的策略:
- 自动化与智能化:引入自动化设备和智能管理系统,减少人为操作的误差和变动。自动化系统可以帮助平衡生产负荷,确保每个环节都在最佳状态下运行。
- 数据驱动的决策:利用FineBI等商业智能工具进行数据分析,实时监控生产线状态。通过数据驱动的决策,我们可以更精准地识别问题和机会,优化生产计划。
- 人员培训与激励:确保员工掌握最新的技术和操作流程,提高生产效率。此外,激励机制可以鼓励员工积极参与优化生产流程的活动。
- 精益生产原则:精益生产的核心在于通过消除浪费来提高效率。通过持续改进和价值流分析,生产线可以实现更高效的负荷管理。
- 柔性生产规划:制定灵活的生产计划,根据市场需求和生产实际情况调整生产策略,避免过度生产或库存积压。
- 设备维护与升级:定期维护和升级设备,确保其在高负荷下稳定运行。这不仅能延长设备寿命,还能提高生产线的可靠性。
通过以上策略的实施,再结合FineBI等工具的应用,企业可以在不增加大量成本的情况下,实现生产线负荷的优化,提高整体竞争力。